Different Types of Commercial Metal Roofing & Material Options
As a broad category, commercial metal roofs encompass a broad range of materials, panel types, pitches, and fastening options. Each decision comes with its own set of pros and cons that affect the cost, appearance, and estimated lifespan of the roof. In this article, we differentiate between various types of metal roofs so you can find the best option for your budget, environment, and building needs.
Keep reading or use the links below to learn more about various types of metal roofs:
Why consider metal roofs as an option in the first place?
Metal roofs can cost more than other commercial material options like asphalt, BUR, and spray polyurethane foam (SPF). However, many architects decide it is well worth the added expense due to its many advantages, making it a commercial roofing trend continuing to rise in popularity. To begin with, the expected lifespan of metal roofs can be between 40 to 100+ years, depending on the type of alloy used; comparatively, other commercial roofing options like asphalt are expected to last a maximum of 20 years. Metal’s ongoing maintenance needs are also comparatively light due to their inherent durability and longevity.
Metal roofs are also more environmentally-friendly than many other types of roofing, starting with the fact that the materials can be fully recycled after use. Additionally, the metal’s ability to reflect UV rays away from the building results in reduced energy usage dedicated to cooling.
Most importantly, metal roofs are well-equipped to face turbulent weather, whether that be high wind speeds, debris, wildfires, or ongoing precipitation. However, some types of metal roofs are better suited for specific environments than others, which we’ll explore further within below talking points.
What to factor when choosing a metal roof type and material
Before exploring the different metal roof types and common commercial materials, its important to understand the following about your upcoming project:
Budgetary confines - Your choice of design and the specific alloy will greatly influence costs by thousands of dollars, especially if you’re budgeting for a larger commercial project. Keep in mind not only the price of materials but also related shipping and installation expenses. After all, some commercial roofing materials are less available and may need to be sent from great distances, and some systems require longer installation times and specialized laborers.
Environmental demands - A metal roof installed in hot, dry Nevada will have dramatically different needs than one in moderate Missouri or hurricane-prone Florida. Take into account positioning near the coast, precipitation patterns, frequency of strong winds, and the level of need for innate cooling roof elements.
Tolerance for ongoing maintenance - Metal roofs with higher upfront costs tend to require less maintenance over time (and vice versa). This is particularly valuable for larger commercial buildings, as one point of vulnerability could signify the entire roof must be assessed.
The desire for longevity - The good news is that metal roofs provide admirable lifespans with even the cheapest options with the expected minimum being forty years. However, that number can grow to 100+ years if you choose commercial material options like zinc or copper (which require greater upfront costs).
The general aesthetic - Metal can take on a diverse number of shapes and hues based on the specific roof type, how it's fabricated, and how it interacts with the surrounding environment. Some systems appear effortlessly modern (like standing seam) while others can evoke traditional charms (like metal shingles).
Standing seam metal roofing
This particular type of metal roof earns its name by having panels tightly affixed to one another with raised seaming typically 1-3” tall. This means that the components clip together without any visible fasteners, yielding a smoother appearance and tighter weatherproofing. Another benefit of the standing seam design is that most roof clips accommodate the natural expansion and contraction of the panels due to dramatic swings in temperature, reducing the accumulated wear on the fasteners.
Commercial builders will have to choose between standing seam systems that automatically snap together and those which require mechanical seaming. While the latter type requires more work, it ultimately reinforces the roof against heavy winds.Plus, unlike some other metal roof options, standing seam systems accommodate low slope and flat roofs with pitches as small as 1:12 pitch.
Standing seam metal roofs will cost more than other commercial types regarding both materials and installation. However, they require less ongoing maintenance over the years and are thicker than corrugated sheets and shingles, making them less likely to be damaged by debris or workers’ boots.
SHOP FOR METAL ROOF CLIPS AND STANDING SEAM FASTENERS
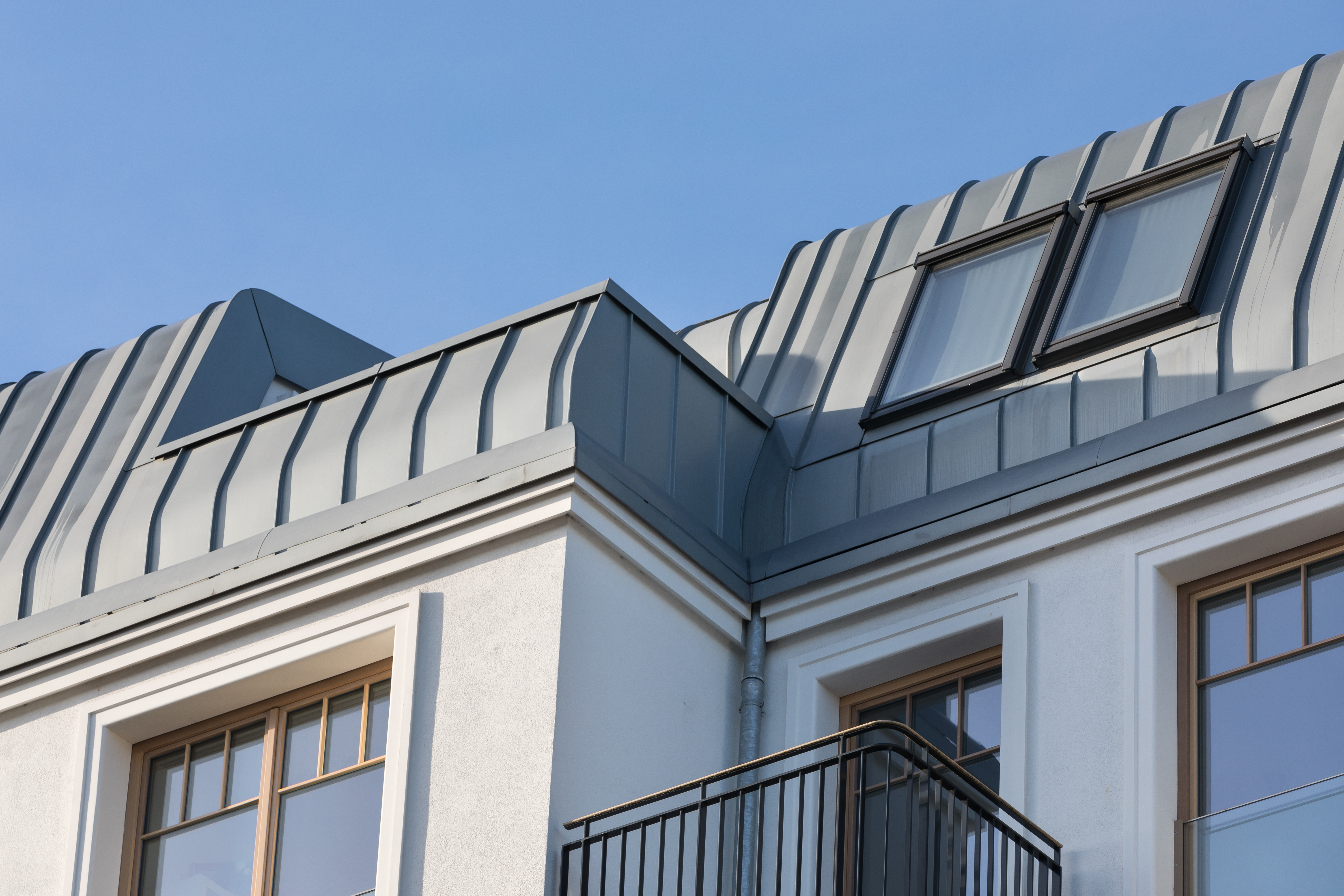
Corrugated metal roofing
If your environmental and aesthetic needs don’t require the premium prices of standing seam systems, a corrugated metal roof might be your best option. Made from sheets of rolled metal fabricated to take on a wavy silhouette, this type of roof is almost twice as affordable as its standing seam counterpart for both the costs of materials and installation.
In addition to the distinct ridges of the metal panels, another noteworthy element of this roof type are the exposed fasteners. As we explore in Roofing fasteners: exposed or concealed, this results in more affordable screws, less labor time, and reduced costs when repairs are needed.
However, there are also downsides to the exposed fasteners, starting with the fact that direct exposure to the elements leads to an increased likelihood of corrosion and leaking. Additionally, their fixed grips don’t accommodate the natural shifting of panels (as clips do), contributing to increased stress on the screws. All this means that you will need to replace exposed roofing screws more often than you would concealed fasteners.
Lastly, corrugated metal roofs cannot work with lower pitches, requiring a slope of at least 5:12.
Metal shingle, tile, and slate roofing
As the names imply, these types of commercial roofing take on the appearance of classic shingles or tiles but reap the advantages of employing metal. They can take on a surprisingly diverse range of colors and shapes to mimic traditional materials making them a common choice for re-roofing projects or residential projects.
Depending on the materials the metal is meant to mimic, the metal imitation may actually be cheaper than the genuine textile (such is the case with Spanish clay tiles and slate). However, the enhanced aesthetic of this design option leads to it being more expensive than even standing seam roofs, making it less popular for commercial builds.
So, how do metal shingles and tiles perform against the elements? They offer greater protection against leaks and corrosion than corrugated roofs but don’t quite measure up to the performance of standing seam options. Additionally, this type of roofing is thinner than standing seam panels, making them more susceptible to damage. Lastly, similar to corrugated roofs, metal shingles and tiles cannot be applied to low-slope buildings; more specifically, the International Residential Code (IRC) specifies a minimum 4/12 pitch (4 inches of vertical rise for every 12 inches of horizontal run) for a clay or concrete tile roof, except that a pitch as low as 2-1/2/12 is allowed when two layers of underlayment are applied.
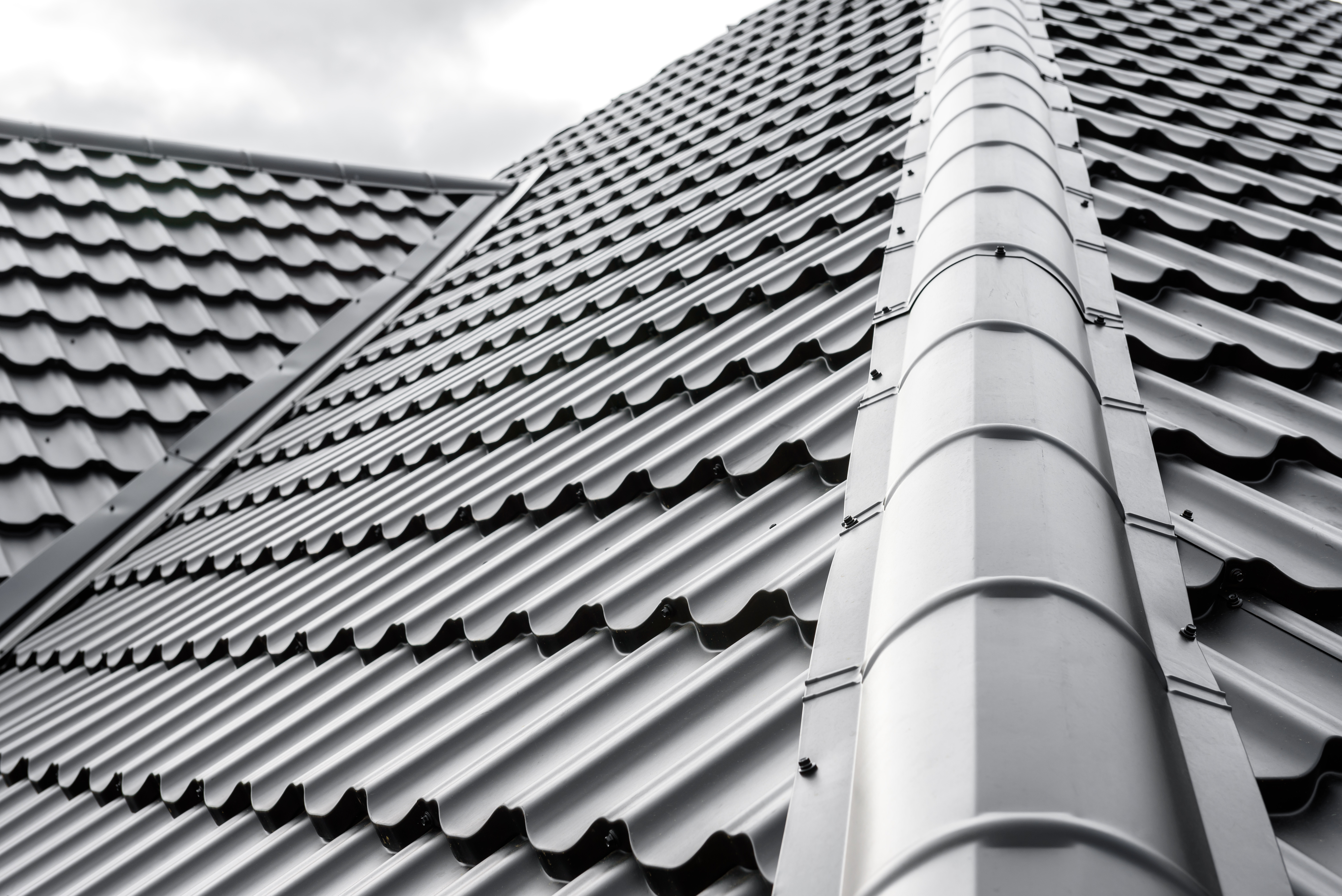
Material Options for Commercial Metal Roofs
It should come as no surprise that “metal” is a far-reaching classification of commercial roofing materials that covers diverse price points, strengths, and levels of corrosion resistance. Below, we breakdown the pros and cons of options most likely to be utilized:
Steel in Commercial Roofing
Steel is, hands down, the most popular material for commercial metal roofing, so much so that some people use the terms “steel roofing” and “metal roofing” synonymously.
Steel roofing won legions of fans because of its undeniable strength, no matter what you throw its way (fires, termites, high winds, etc.). Additionally, steel roofs are generally more affordable than other metal roofing materials, both in regard to upfront costs and ongoing maintenance needs.
However, for all there is to love about steel as your commercial roofing choice, there are some points that may make you pause. For starters, its resistance against corrosion (though respectable) is not as strong as some of the more expensive metal materials, like copper or zinc. Relatedly, its lifespan, a respectable 40-60 years, is shorter than what’s offered by the more expensive metal roof types. Moreover, it's heavier than most other metal options, placing increased strain on the structure.
Aluminum in Commercial Roofing
Aluminum’s lightweight nature is both an advantage and disadvantage in its use as a roofing metal. Benefits of aluminum include:
The reduced weight makes it particularly malleable and puts reduced demands on the building below to support the roof’s mass
Overall strength that rivals heavier metal roof options
Impressive resistance against rust, even in environments with considerable moisture or corrosive elements like oceanic salt air.
These benefits are not without their downsides, starting with elevated costs when compared to steel. Additionally, though aluminum is incredibly strong considering its overall lightness, it still is more susceptible to dings than other metal roofing materials. For such reasons, it may be more difficult to find than steel and is offered with fewer color options.
Aluminum is more likely to be used in metal roofs with a pitch of at least 3:12 (just over 14 degrees). What’s more, its superb corrosion resistance makes it particularly fitting for coastal buildings.
Zinc in Commercial Roofing
We’ll cut to the chase—zinc is one of the more expensive options for metal roofs, but for good reason. Over time, it produces an attractive patina of light gray or even bluish that further reinforces the roof against corrosive elements (take note, the onset and tint of patinas can be hard to predict).
Additionally, zinc is fully recyclable and utilizes less-than-average fuel in its creation. As for those upfront costs, zinc roofs help compensate over the decades due to their long lifespan and low maintenance needs.
With all the advantages of choosing a zinc roof, costs tend to be higher. However, the initial price tag is not the only downside you should consider with this type of metal roof. Availability is extremely limited for US builders, meaning that shipping costs will further eat into your budget. Additionally, because of its lack of Stateside popularity, it will be tricky to find contractors experienced with this particular type of metal roof option.
Copper in Commercial Roofing
Copper rivals the cost of zinc metal roofs due to its similar properties (the striking aesthetic and emergence of a patina). Copper offers a particularly long lifespan that can extend to a century or more, and offers peak corrosion resistance that can withstand even the roughest of environments. Better still, it is lighter than steel roofing options.
So what are the downsides of copper for metal roofs? First and foremost, it is one of the most costly metal roof options on the market. Additionally, because it is lighter than its steel counterpart, it is more likely to be damaged by debris. For this reason, properly installed copper will be thicker than steel types, further driving up expenses.
The good news is that copper is more available to American roof builders than Zinc, but there’s still a limited number of distributors.
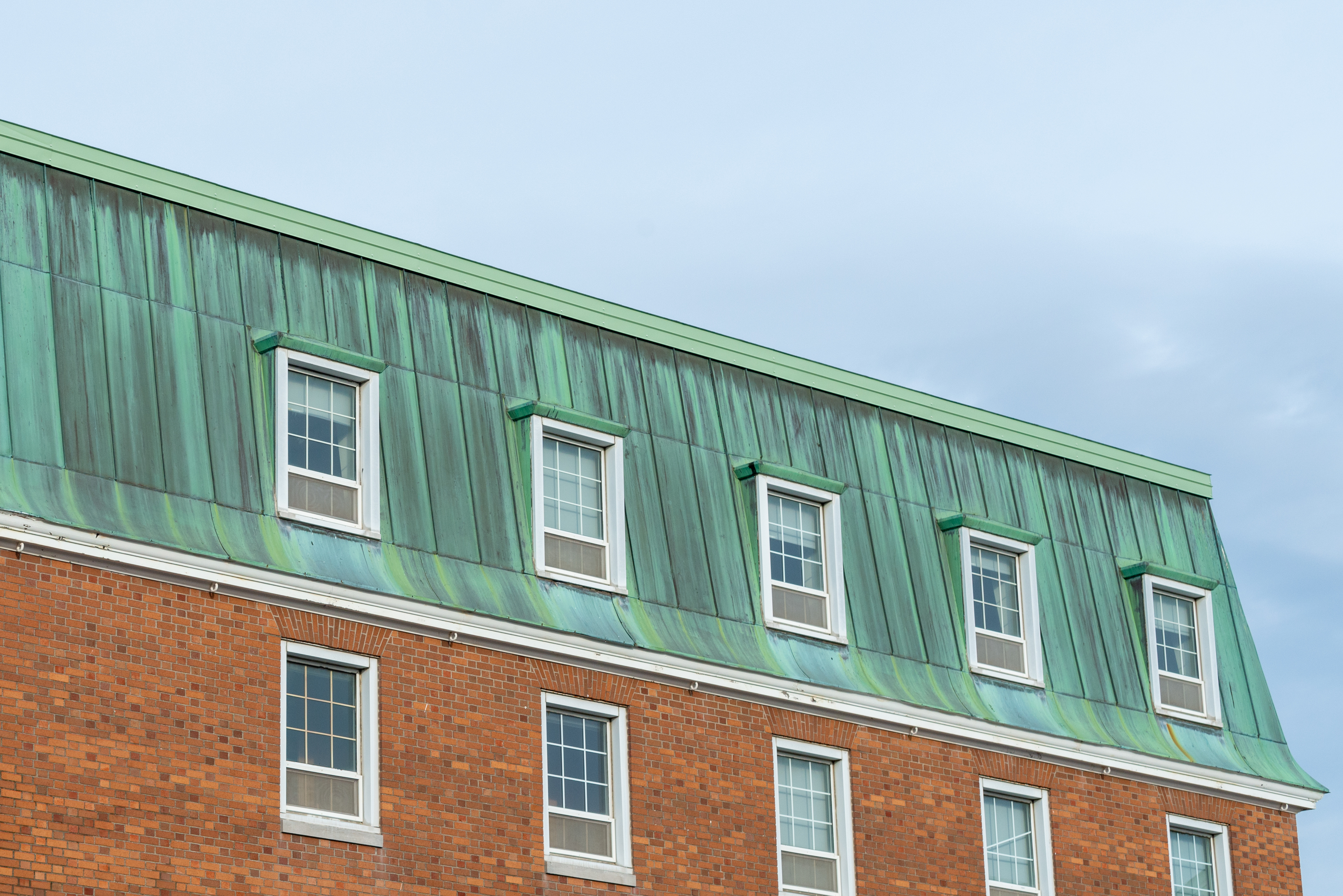
Key Takeaways About Different Types of Metal Roofs
In summary, there is no one commercial roofing material or type that is undeniably better than the rest. Rather, the best option for your build comes down to the budget, environmental needs, and tolerance for ongoing maintenance.
Another important takeaway is that your choice of fastening system (standing seam vs. exposed) and the fasteners themselves play a large role in the success of the build. That’s why it’s important to partner with a manufacturer with a proven track record and communicative customer service, like SFS. Over our 55+ years of experience, we’ve supplied more than 26 billion fasteners to commercial projects, not unlike yours. Moreover, we continue to innovate so we can confidently say our products are the best on the market.
Contact us at 610-376-5751 to discuss how our team can help you with your next commercial project.